PLASTISOL
speciality materials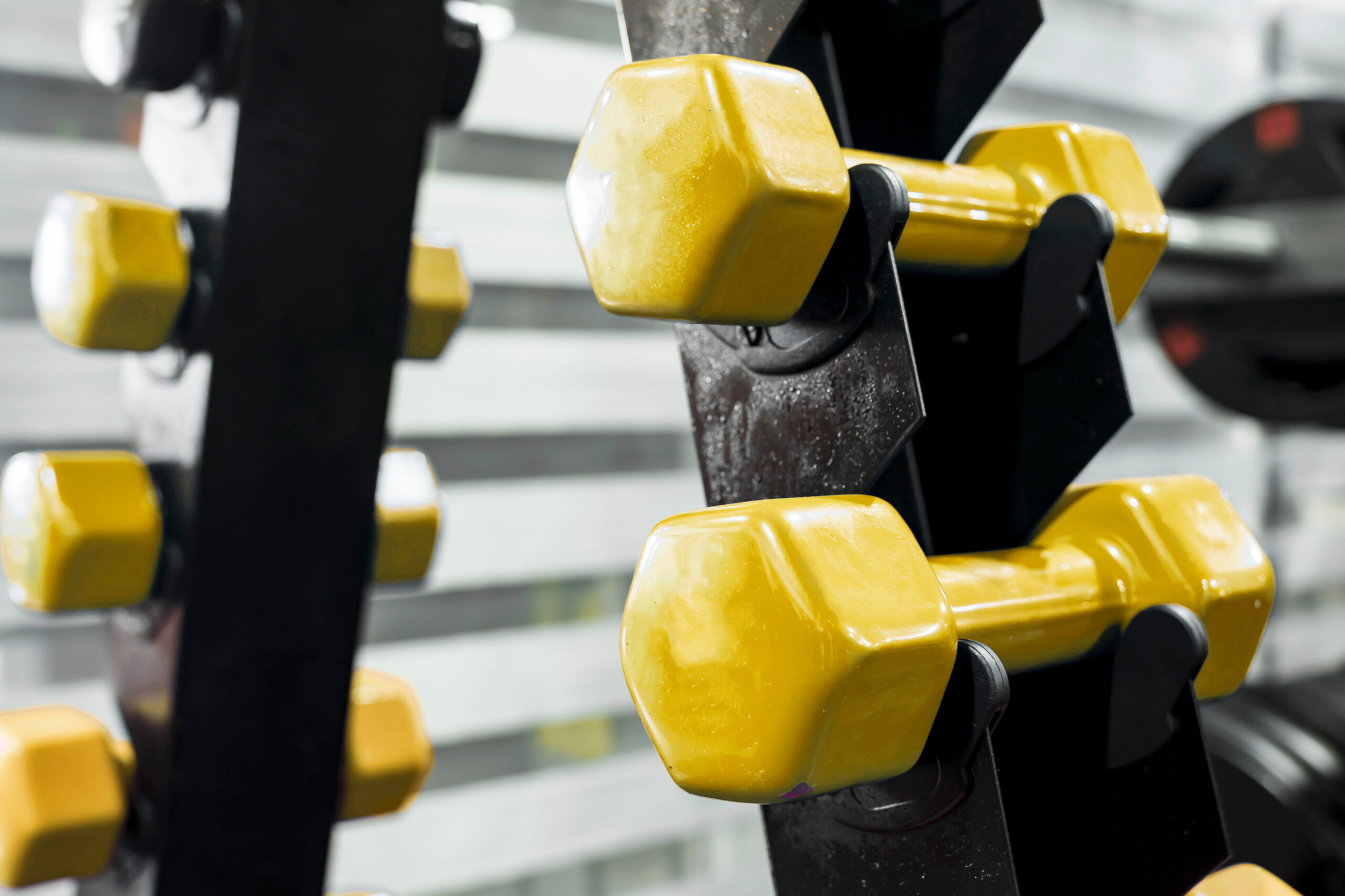
OVERVIEW
The liquid vinyl specialty material.
Many everyday products require durability, functionality, and high-performance characteristics. Manufacturers often need versatile physical and resistance properties for molding or coating a variety of products.
PLASTISOL is a liquid form of vinyl that is cured by heat to form a solid end product. Properly cured PLASTISOL can offer a wide variety of physical properties & attributes, all depending on the formulation.
How does it work?
PLASTISOL is a liquid dispersion of PVC resin in a plasticizer. It is formulated based upon processing parameters, end-use applications, and desired
product specifications. By utilizing an extensive group of raw material additives, PLASTISOL is an incredibly versatile polymer choice.
Main features
- Can be custom formulated for a wide variety of market applications and processing methods.
- Optimized for applications include dip coating, dip molding, rotational molding, slush molding, hot melts, inks, textile coatings, and adhesives.
- Performs as a protective, functional, and decorative coating for a variety of end products with many types of resistance properties available.
- Formulated without solvents and low in Volatile Organic Compounds (VOCs)
COLOR OPTIONS
Color reference chart
Get inspired by a broad range of standard colors.
Visit our Color Finder page for inspiration.
Custom formulations
Talk to your coating expert regarding custom formulations to fit your exact needs.
RESOURCES
Compliance
PLASTISOL can be formulated to be compliant with certain guidelines.
Ask our experts to see what different types of compliance, certification, or accreditation are available for your product.
PROVEN PERFORMANCE
PPLASTISOL can be tested on demand for various properties.
- Tensile
- Tear
- Elongation
- Density
- Gelation Temperature
- Flame Retardancy
- Fineness of Grind
- Gloss
- Viscosity
- Dielectric Strength
- Hardness
- Bond Strength
- Heat Ageing
- Phthalates
APPLICATIONS & USES
Dip Coating
Dip coating is a process by which substrate material is submerged in conformal coating, then taken out and allowed to drip dry. Once the excess coating has drained, the substrate material is further dried using one of a variety of techniques.
CONSUMER GOODS & APPLIANCES
- Wire Items
- Glove Coatings
COMMERCIAL & INDUSTRIAL
- Latches & Levers
- Handles
- Tools
- Chains
Dip Molding
Dip molding is a process that’s used to create products or parts with a hollow interior. It involves submerging a mold in a bath of heated PLASTISOL and allowing it to cool. Once cooled, the hardened exterior is separated from the mold. Because the mold fills the space inside the plastic, dip molding creates products or parts with a hollow interior.
CONSUMER GOODS & APPLIANCES
- Grips
- Plugs
- Bellows
- Sleeves
- Closures
- Fishing Lures
Hot Melt
This PLASTISOL application involves heating to a molten state, and either poured or injected into a cold or room temperature mold. When cool, the hot melt is transformed into a soft, rubbery product, at which time the finished part can be removed from the mold.
ARCHITECTURAL
- Artificial Stone Wall
- Fishing Lures
Rotational Molding
Rotational molding, commonly referred to as roto-molding, is an application technique used to produce large hollow, seamless, and double-walled parts. It is a three-stage process that involves a mold on a rotating frame, a heating chamber, and a cooling chamber. Rotational molding is a non-pressure molding process, which makes the tooling of the molds less expensive since they do not have to endure the stress of being pressured
CONSUMER GOODS & APPLIANCES
- Toys
- Boat Fenders
- Sports Balls
- Mannequins
- Novelty Items
Slush Molding
The basic process of slush molding involves exposing a hollow mold to heat, filling a hollow mold with PLASTISOL, gelling an inner layer or wall of PLASTISOL in the mold, inverting the mold to pour out the excess liquid plastisol or unfused powder compound and then heating the mold again to fuse the vinyl compound which remains in the mold. The mold is then cooled, and the finished part is removed. Slush molding can be a simple hand operation for limited production, or an elaborate conveyorized system for long runs.
CONSUMER GOODS & APPLIANCES
- Boots
- Masks
- Toys
Casting & Adhesives
The same techniques used in dip molding and dip coating can be utilized to cast solid objects made of PLASTISOL. Sharing similarities with injection molding, PLASTISOL is poured into a mold and heated to cure. The process is highly customizable including cutting out shapes and adding adhesive backings.
CONSUMER GOODS & APPLIANCES
- Air Filters
- Mats
COMMERCIAL & INDUSTRIAL
- Ceramic Tile Dot Mountings
Foam Molding
PLASTISOL foam molding can be used for a variety of applications. It be used in a variety of processes including hot dipping applications, open and closed molds, and roll coating. Upon fusion, the finished product will have chemically expanded open or closed cells. Foam products can also be produced by mechanical frothing.
CONSUMER GOODS & APPLIANCES
- Air Filters
- Mats
- Grips & Tools
- Textiles
Spray-On
PLASTISOL can also be spray applied and then heated to form a protective or decorative coating. This process is usually reserved for large or dimensionally challenging objects which are too large or unwieldy to coating with other processes.
COMMERCIAL & INDUSTRIAL
- Tank Linings
- Battery Trays
Customized
PLASTISOL is a fully customizable solution, from color, formulation, properties, and characteristics.
Ask an expert for all your PLASTISOL compound requirements
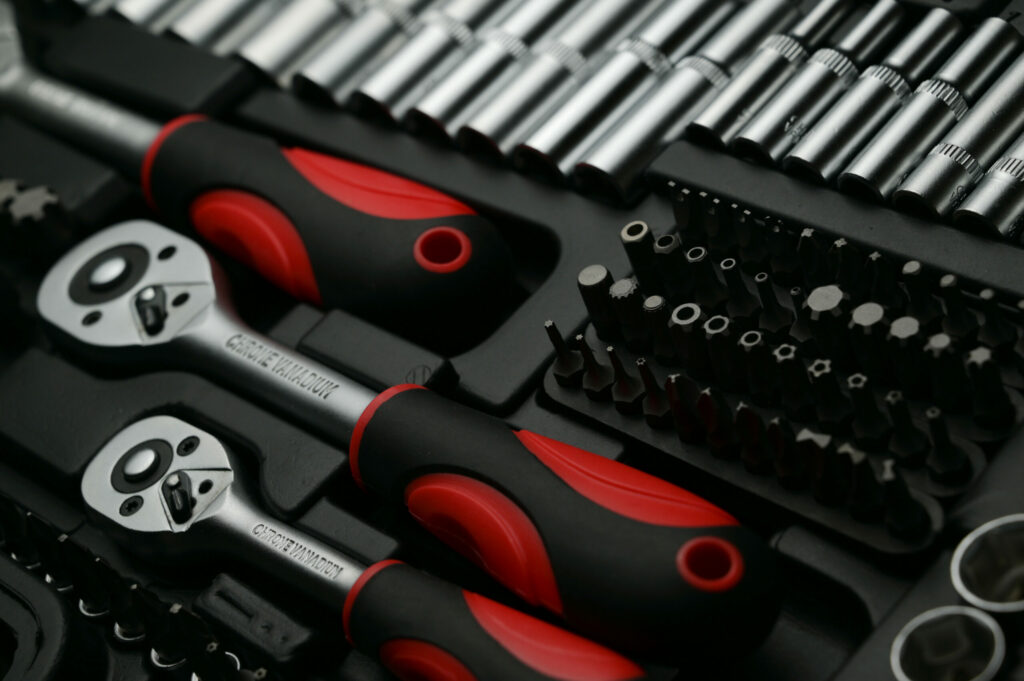
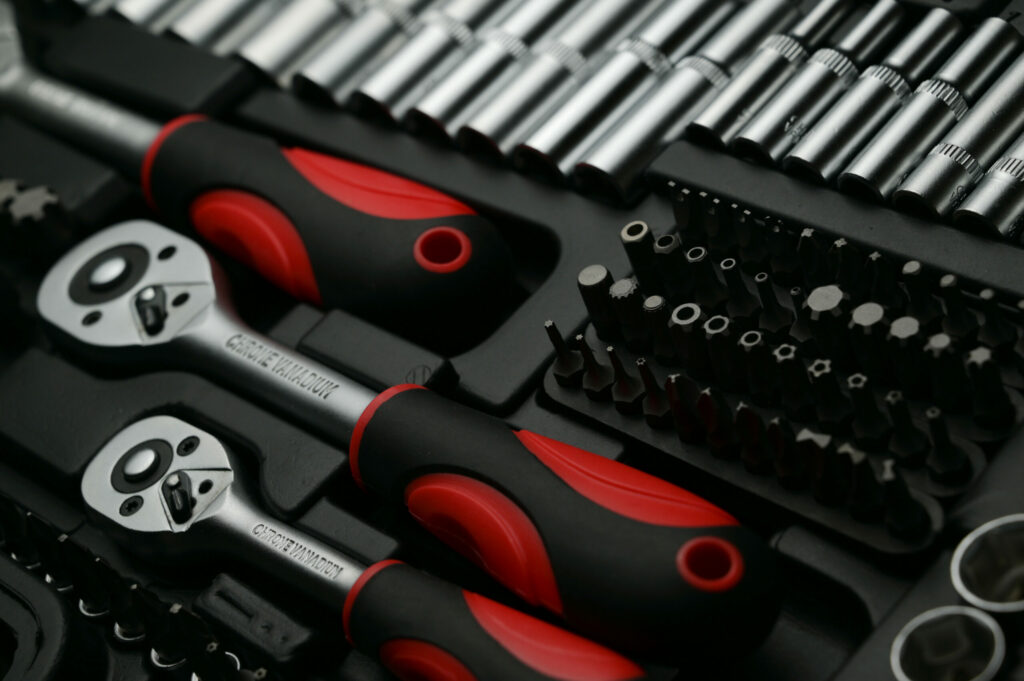
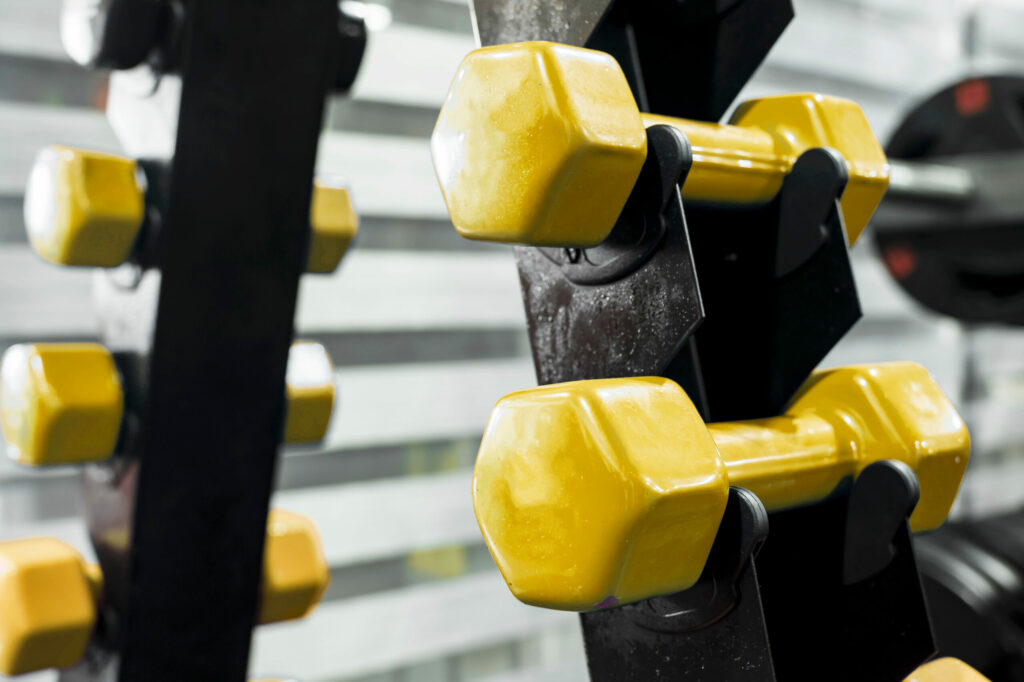
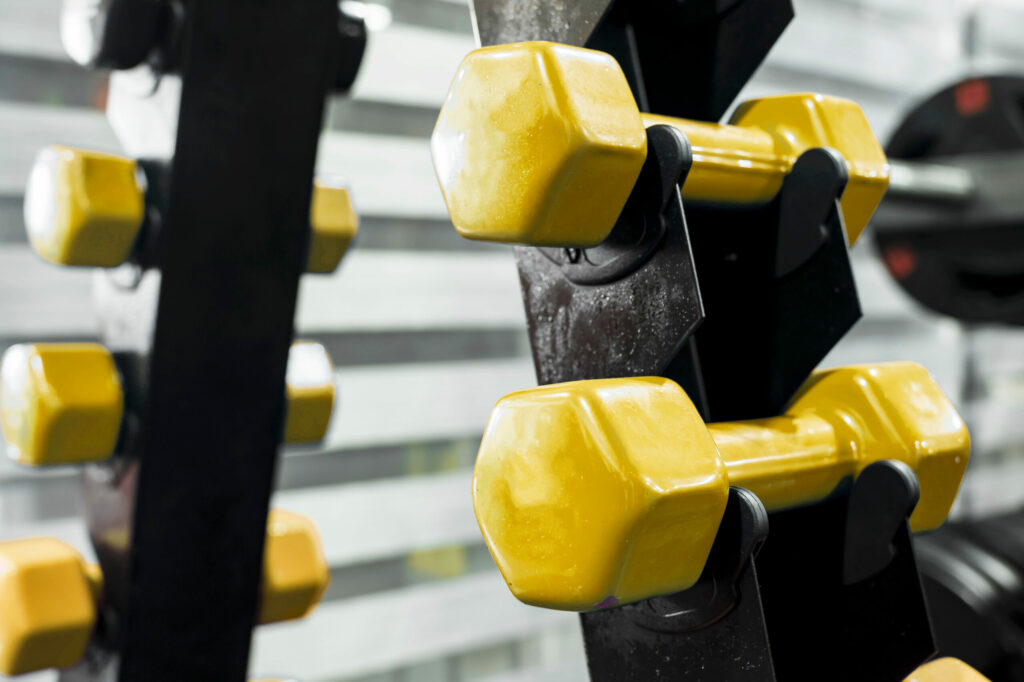

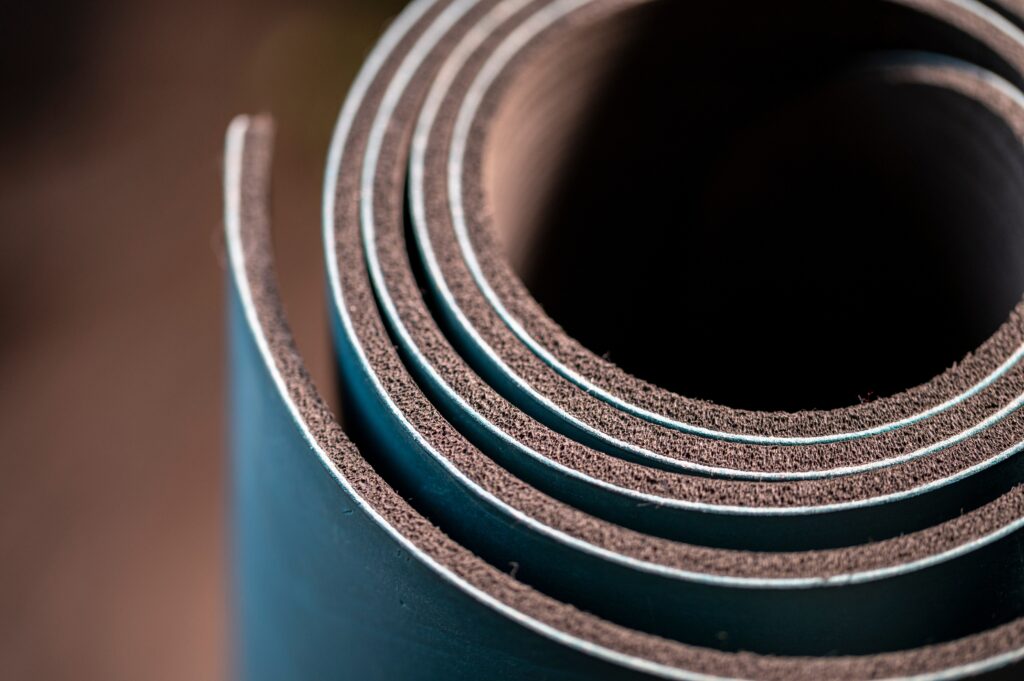